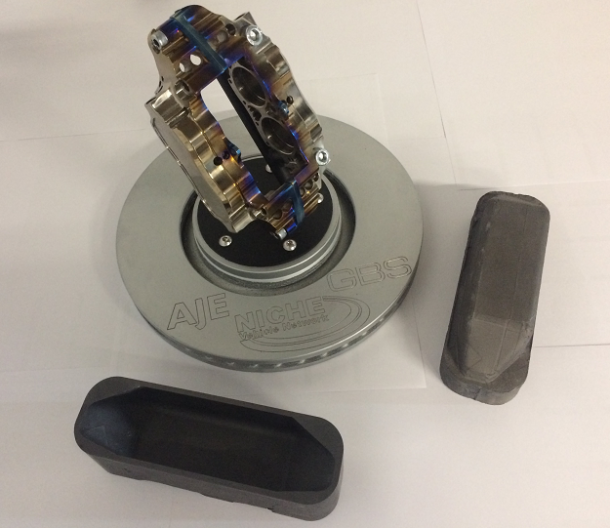
Collaboration and Investment leads to new technologies
About AJE Powertrain
AJE Powertrain were established in 2016 and have an office and workshop premises in Preston, Lancashire. Combining the simulation, testing and product development expertise of its directors enables it to provide engineering services to the niche and mainstream automotive industries, especially considering tightening emission legislation. Their main areas of expertise are in the development & application of lightweight materials and improvements for energy efficiency (with both ICE and electrified powertrains).
The personnel within AJE Powertrain have a diverse range of automotive engineering skills, with experience from numerous major OEMs in both powertrain and component level development (at technical engineering and project lead levels). These experiences include development of new technologies, from concept to production; design and development of existing hardware for alternative duty / performance; resolution of manufacturing issues to assist volume constraints and quality improvements (from raw parts to assembly processes). They also have considerable experience in simulation and physical testing techniques and their application regarding legislation and product durability.
Collaboration and Investment leads to New Technologies
For the project, AJE Powertrain partnered with Great British Sports Car Ltd. They are a specialist sports car OEM and manufacture most components (75%) in-house from raw materials through to complete registered turnkey vehicles. This includes GRP body panels and carbon fibre body panels.
Great British Sports Cars Ltd have a rapidly growing reputation within the market for producing vehicles which provide outstanding value for money and have recently separated the component car and turnkey elements of the business with a view to enhancing their position as a recognised low volume manufacturer.
The purpose of the Niche Vehicle Network partially funded project NV17-PC116 Low Cost High Performance Titanium Brake Caliper was to further develop a new manufacturing process for titanium (Ti6Al4V) components for the automotive industry, initially aimed at low volume, high value manufacturing companies such as those represented by the Niche Vehicle Network.
The benefits of Ti6Al4V over conventional materials are well understood. The material has a high strength to density ratio enabling mass reduction, it has good corrosion and temperature resistance and it possess a ‘technology status’ as it is primarily used in Aerospace, making it an ideal material for the niche vehicle markets.
The process had been proven on a laboratory scale by the University of Sheffield (UoS) but there was a need to develop it for use in mainstream manufacturing (more usable shapes and processing techniques). An earlier feasibility study by AJE Powertrain identified brake caliper housings as a good candidate for this process. Great British Sports Cars Ltd (GBS) already manufactured brake calipers in-house to their own design and so a collaboration was formed, to produce brake caliper housings in titanium by the FAST process, then machine, assemble and test to prove the concept.
What support did AJE Powertrain receive?
The Consortium were able to access help and financial support from the Niche Vehicle Network, CENEX, The Advanced Propulsion Centre and Innovate UK, UoS and Kennametal UK Ltd.
Working with the NAA in the supported programme for Lancashire businesses, funded by The Local Enterprise Partnership, ensured that they were made aware of funding opportunities and are already awaiting news on another project.
Future Developments
The work completed so far represents a major step forward for this technology. Until now only laboratory scale work has been completed and no working components had been manufactured using the FAST titanium process. The consortium believes this process is at a stage where it could be taken to a production ready solution in a short time with the correct level of support. Ideally the feedstock should be waste aerospace titanium, as this will reduce the piece costs to an acceptable level. There are some small development steps needed to be able to use this but most of the required development is around productionisation / process streamlining to enable small volume runs of components from existing machines using the known tooling & processing parameters.
The potential for the FAST process with titanium to produce parts for the niche automotive sector is evident from the results of this project. It is hoped that support can be obtained for both consortium members to progress this exciting field of manufacturing for the UK.