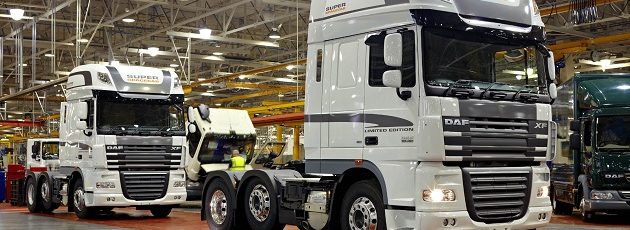
LEYLAND TRUCKS IMPROVES ASSEMBLY PROCESSES THROUGH THE APPLICATION OF LEAN MANUFACTURING
The activities were carried out within a specific assembly team and resulted in a 25% reduction of in-process defects, waste being decreased, quality being enhanced, and assembly speeds improved as a result of introducing new lean procedures
PROJECT
Lean Manufacturing Mentoring.
BACKGROUND
Leyland Trucks manufactures the full range of DAF Trucks – from 7.5 to 44 tonnes – at its facility in Leyland. All vehicles are produced on one line at a rate of 20,000 per year.
The facility operates in line with the Paccar Production System (PPS) and Leyland Trucks is one of the best performing assembly plants within the Paccar family. In addition, Leyland Trucks has a Queen’s Award for Enterprise, it has won the IMechE MX award in two consecutive years, and has recently been awarded the Bronze Shingo Award.
Leyland Trucks can demonstrate strong continuous improvement, grounded in Six Sigma, and the company is always striving for new ways to improve its business.
PROJECT AIM
Leyland Trucks was looking to target productivity and quality improvements of a minimum of 10% by implementing advanced lean manufacturing mentoring.
DRIVE FOR CONTINUOUS IMPROVEMENT
With the number of vehicle specifications and options, maximising efficient production is a significant challenge, from both an assembly and material flow perspective.
Leyland Trucks wanted to create a template for the enhanced, sustainable deployment of advanced lean techniques within the Paccar Production System. Specific assistance was sought in the facilitation and mentoring of staff in key aspects such that they could roll out the techniques across the facility.
The intention was to enable a dedicated team to support this project, with specific mentoring support in work standardisation, 5S, visual team processes and lean material flow.
APPROACH
Industry Forum provided mentoring for the business improvement activity, with financial assistance from the Northwest Automotive Alliance (NAA) Business Excellence programme. The activity focused on the identification and elimination of waste from manufacturing operations in a specific cost centre with a team of 11 operators. The project was resourced by Leyland Trucks to include five permanent team members each from different areas of the business to provide a broad range of knowledge and abilities. The time period for the improvement activity was set at 40 days to provide sufficient time for all the phases and to maximise operator involvement as much as possible.
Key objectives of the activity were as follows:
- Improve visual management
- Create standardised work
- Have an impact on key metrics – Defects per Unit, Inventory Accuracy and Truck Hours
- Implement a 5S standard
- Sustain the changes
OUTCOMES
The activity successfully implemented changes within the cost centre, achieving improvements in all of the key objective areas. An important outcome of the activity was the implementation of a cost centre team board to present and record information relevant to the team. This became a focal point for the team and has been extended to other cost centres in the business.
The outcomes of the project included improvements in the following areas: defects per unit for air con and clutch pipe assignment; process time for radiator assembly; inventory accuracy – by part location and by quantity. In particular, a focused improvement on the assembly process for clutch pipe assignment and the reduction of waste brought about a 25.9% decrease in the number of reported defects.
John Keegan, PPS Co-ordinator, Leyland Trucks Ltd, says “The support from the Northwest Automotive Alliance (NAA) Business Excellence programme has enabled us to work with our team to implement practical, common sense solutions, which have resulted in significant outcomes in a number of areas such as a reduction in defects and improvements in productivity.”