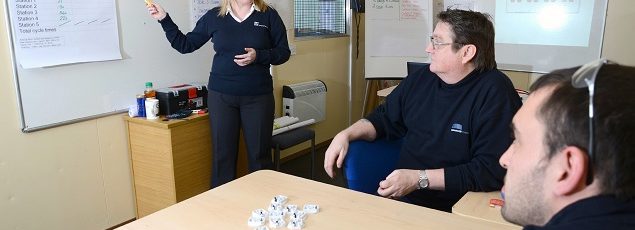
ELE ADVANCED TECHNOLOGIES ACHIEVES SAVINGS OF OVER £35,000 FROM BUSINESS EFFICIENCY IMPROVEMENTS
Project results in significant cost savings for ELE following the identification and elimination of wasted time on the production line
PROJECT
Improvement Masterclass and Business Processes Value Stream Mapping.
BACKGROUND
ELE Advanced Technologies manufactures precision-engineered automotive turbocharger components, with a strong reputation in the lower volume, high variety market for commercial vehicles and passenger cars. The company has the capability to produce a range of turbocharger components, including turbine housings, centre housings (also known as bearing housings), and integrated manifolds. ELE’s customers include the world’s leading turbocharger suppliers such as Honeywell, and the company’s products can be found in cars ranging from Land Rovers to Bentleys, as well as commercial vehicles. In addition to manufacturing components for automotive turbochargers, ELE also produces components for industrial gas turbines and aerospace.
PROJECT AIM
To carry out Value Stream Mapping in order to improve the efficiency of ELE’s business processes
NEED FOR IMPROVEMENT
Analysis of downtime in ELE’s production areas showed that at least 16% of downtime was directly attributable to machine set-up. This increased recently as a direct result of customers reducing batch size requirements, as they focused on reducing the cost of inventory and aimed for JIT delivery. ELE had created an initial current state Value Stream Map (VSM), but the future state had not been produced and there was no implementation action plan in place.
APPROACH
Through the Northwest Automotive Alliance (NAA) Business Excellence programme, Industry Forum (IF) won a competitive tender to provide consultancy support to ELE. An IF engineer worked alongside a team of ELE personnel to facilitate a Masterclass and a detailed study of the current set-up process, on a twin-wheel grinding machine, was carried out, utilising video footage of machine change-over activities. Based on the analysis, a plan was formulated for how machine set-up time could be saved, ensuring that results could be replicated for other machines. A practical implementation workshop was subsequently conducted to reduce the changeover time.
To carry out set-up procedures, employees were walking over 500 metres to get items such as the correct tools, so new simple procedures have been put in place to eliminate movement and associated time wastage and achieve a more organised approach.
OUTCOMES
Based on the results from the initial item of machinery, the project achieved a timesaving improvement of 50%. Subsequently the same principles were applied to a second machine and in total, to date, this has resulted in cost savings of over £35,000. However the same approach can be transferred to other areas of the business, and therefore, over time, further savings are expected. ELE was considering adding a weekend shift to operate one of its machines, but the efficiency improvements achieved by the project has eliminated this need.
Peter Calderbank, Operations Director, ELE Advanced Technologies Ltd, says: “The NAA Business Excellence programme introduced us to Industry Forum, which has been an excellent organisation to work with, and the funding allowed us to invest in a quality programme, which has produced very impressive results. This project has been a real success and I would strongly recommend the Business Excellence programme to other companies that want to achieve efficiency improvements.”