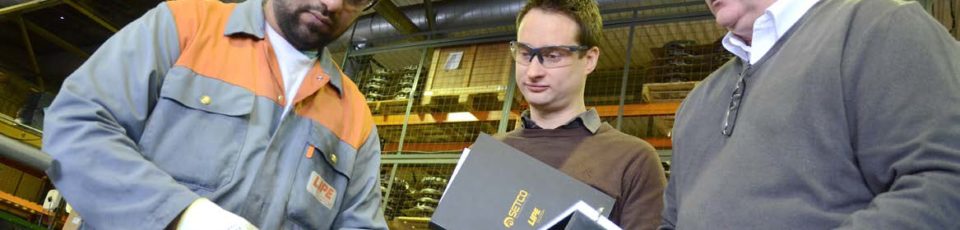
SETCO IMPLEMENTS NEW HEALTH AND SAFETY SYSTEM TO HELP BUILD WORLD-CLASS BUSINESS
Commercial vehicle clutch manufacturer targets new OEM customers having established an OHSAS 18001 compliant system
PROJECT
Implementation of OHSAS 18001, an international occupational health and safety management system specification.
BACKGROUND
Setco Automotive (UK) Ltd was established in 2006, previously trading as Lipe Clutch. The company has a 30-year background in the design, manufacture and distribution of commercial vehicle clutches. The business has successfully expanded, with a wide-ranging base of 250 UK customers, and has developed clutches suitable for a wide range of European applications at competitive rates.
Setco currently serves the aftermarket but has aspirations to supply original equipment manufacturers (OEMs). The company can manufacture specialised one-offs or production quantities to service OEM demand. The facility currently produces between 1200-1600 units per month.
Setco’s ambition is to accelerate the pace of design and development, and take advantage of the brand name and reputation to further develop sales in the European Union with the Lipe Clutch products.
PROJECT AIM
To improve health and safety standards, staff motivation, and, importantly, directly increase sales by meeting and surpassing customer requirements for quality standards.
NEED FOR IMPROVEMENT
One of Setco’s key business goals is to supply OEMs, and the OHSAS 18001 health and safety standard is required in order to do this.
APPROACH
The Northwest Automotive Alliance (NAA) Business Excellence programme supported the project, which was delivered by Smith Consultants. Specific tasks undertaken as part of the project were:
- A new and more concise health and safety manual was issued, in order to be more up to date with the latest business practices and legislation whilst being simpler to implement, review and maintain.
- All risk assessments were updated and improved to make them more effective, whilst also significantly reducing their complexity.
- New company metrics for health and safety were implemented to allow the company to more proactively analyse any trends regarding health and safety risks and effectively implement corrective actions.
- A new health and safety committee has been defined, which now meets regularly to continually improve business practices regarding health, safety and welfare.
- New emergency response procedures have been implemented to reduce risks to personnel and business assets should an emergency situation arise.
- Internal auditors have been trained up, and regular audits of the company’s health and safety policy have been carried out to further ensure that the company is operating in a safe manner.
OUTCOMES
Benefits gained from establishing an OHSAS 18001 compliant system include:
- Demonstration of Setco’s highest standards of health, safety and welfare to its customers, employees and other stakeholders.
- Ensuring continuous improvement of the health and safety system whilst keeping up to date with any changes in legislation.
- Supporting business growth by meeting and surpassing the expectations of potential new original equipment customers.
- Boosting staff morale by demonstrating the company’s commitment to their welfare.
- Improved business practices which are more efficient and effective at reducing risk to the business.
Matthew Kershaw, Operations Manager, Setco Automotive (UK) Ltd, says: “Thanks to this project and the support from the NAA Business Excellence programme, Setco has improved business practices, reduced risk and increased the opportunity for securing contracts from OEMs, which is expected to provide an increase in turnover of around £200,000. This will help to consolidate and grow the business, thus safeguarding existing employees and potentially creating more jobs.”