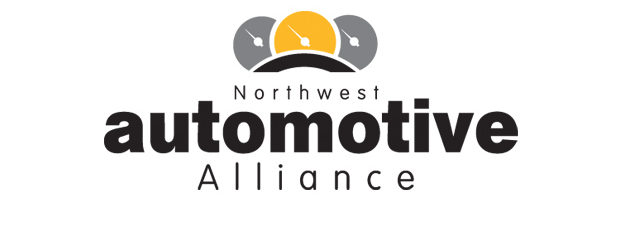
NAA Event: Total Productive Maintenance (TPM) Implementation Seminar, 2 September 2013
Start date: 02/09/2013
Cost: £95 + VAT or Free to NAA Members
This will be a unique opportunity for delegates to understand more about Total Productive Maintenance through a case study presentation; network and explore equipment and management issues with senior staff from the Japanese Institute of Plant Management (JIPM).
Seminar Overview
- The Japan Institute of Plant Maintenance (JIPM) approach to TPM
- Focus on zero accidents, zero breakdowns and zero defects
- Case study from an international organisation
- How to start TPM implementation
- Opportunities for questions and open discussion
- Attendance by Senior Management from JIPM
Who should attend?
The seminar is designed for Senior Management, Functional Managers (e.g. Maintenance, Quality, Safety) and change agents (e.g. Lean, TPM) who are both considering or embarking on TPM implementation within their organisations.
What are the objectives?
The seminar is designed to give delegates an appreciation of the JIPM “Pillar” approach to TPM, demonstrating how TPM can be used to recognise and reduce losses, delivering sustainable business improvement.
The seminar will cover:
- What TPM is, how it will align to your business strategy and other improvement initiatives such as Lean
- The pillars of TPM and how they can drive the elimination of losses
- How to deploy TPM within your organisation
The seminar will be held at Industry Forum Learning Centre, Birmingham on 2nd September 2013, starting with registration at 8.30am and finishing at 1.15pm with time afterwards for networking. Places are strictly limited and allocated on a first come first served basis.
How do I register?
The nominal price is £95 + VAT per head, inclusive of lunch, refreshments and access to the seminar materials, however this is free to NAA members if they book their place through: ross.mcfarlane@industryforum.co.uk