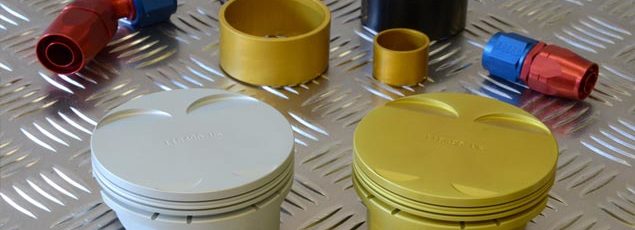
FUNDING ALLOWS CAMCOAT TO SET UP THE FIRST DIAMONDYZE CERAMIC ANODISING PRODUCTION LINE OUTSIDE NORTH AMERICA
Revolutionary new process gives materials such as aluminium greater strength, better appearance and corrosion resistance
PROJECT
Camcoat DiamonDyze ceramic anodising production line
BACKGROUND
Camcoat Performance Coatings Ltd is a company that has been established for over twenty years and, as the European agent for Tech Line Coatings, applies ceramic coatings to exhausts in order to reduce the heat radiated. Camcoat’s customer base is predominantly in the area of high performance production road cars and race cars.
Recently Camcoat became aware of a new process using unique Nano technology, which includes electroplating a ceramic element within the traditional anodising process. This increases strength, improves appearance and gives better chemical resistance, resulting in a longer component life. Typical applications include pistons and highly stressed brackets within the automotive industry and in other transport sectors such as aerospace, maritime or rail. There is currently no other company in Europe carrying out this process.
PROJECT AIM
To set up a pilot production line for a new electroplating process for ceramic anodising, with the aim of introducing a product to market that surpasses the quality of existing products.
NEED FOR IMPROVEMENT
There is currently no company in Europe with the ability to offer coloured hard anodising, so there is a potential business opportunity for Camcoat by providing this service. However in order to do this, a pilot production line needed setting up in order to research and develop the process. This required a significant investment both in terms of equipment and training before the new process could be marketed.
APPROACH
Camcoat has become the only European agent for Tech Line Coatings’ ‘DiamonDyze’ process; in fact Camcoat is currently the only distributor outside of North America. Staff from Canada came over to Camcoat to help set up the new line, and Camcoat staff have since carried out extensive testing and development of the new process.
OUTCOMES
The outcome to date is that the pilot production line has been set up and the ceramic anodising process has been tested. Initial results show that when a coloured finish is applied to materials such as aluminium automotive components using the ‘DiamonDyze’ process, the surface can be rubbed with sandpaper and there is no impact upon the finish or its appearance.
The Northwest Automotive Alliance (NAA) Business Excellence (BE) programme provided mentoring support to Camcoat on establishing an effective production process and testing techniques. The next stage is to expand the new business with Camcoat’s existing automotive customers. The new line will allow samples to be produced and sent to prospects. The aim is to secure a number of initial orders to allow the transition from low to higher volume production. Beyond the automotive industry, the ceramic anodising process could be used for applications such as aircraft structures, ship’s propellers and chemical processing plant.
Peter Carter, Camcoat’s General Manager, says
“The DiamonDyze ceramic anodising process has the potential to offer real benefits to the automotive industry, and beyond. We have taken a significant step to set up the first DiamonDyze production line outside of North America, and we couldn’t have done it without the funding support from the NAA BE programme. I have now been able to have initial discussions with customers of our existing coating process and there has been a high level of interest in the new DiamonDyze process.”