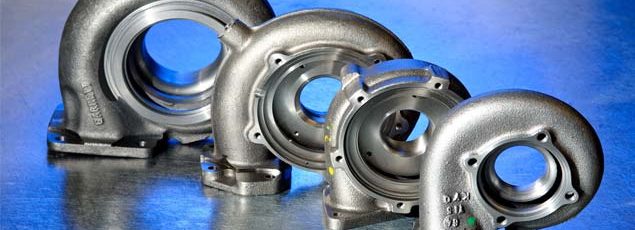
ELE Advanced Technologies Ltd
ELE Advanced Technologies manufactures precision-engineered automotive turbocharger components, working with leading global organisations, with a strong reputation in the lower volume, high variety market for commercial vehicles and passenger cars.
The company has the capability to produce a range of turbocharger components, including:
• Turbine housings
• Centre housings (also known as bearing housings)
• Integrated manifolds.
ELE’s customers include the world’s leading turbocharger suppliers such as Honeywell, and the company’s products can be found in cars ranging from Land Rovers to Bentleys as well as commercial vehicles.
The company has invested heavily in highly advanced machinery in order to be able to produce a wide range of components. ELE has also created leaner processes to produce higher quality components with shorter lead times, and has worked with its employees to develop new, niche processes in non-conventional machining. As a result of this, ELE can provide a competitive solution to both low and high volume production.
ELE aims to pioneer new ways of producing high integrity components for a variety of industries, all demanding flexible production, and it does this by the collaboration of machinists, engineers, scientists and clients, providing innovative solutions for complex engineering challenges.
ELE has the capability to do high-volume work, but the company also has a strong reputation for lower volume, specialist components that other suppliers can’t deliver. ELE also has a proven competitive record which results from cutting edge technology, supported by the best available skills. The company has adopted a structured approach to process development through multi-disciplinary teamwork across the organisation, enabling the business to look at process from a fresh perspective.
ELE empowers its people through the use of statistical techniques to ensure processes remain robust and under control. In this way, the company guarantees consistent dimensional accuracy and competitive production costs.
Alongside its internationally recognised quality accreditations, ELE customer approvals include Alstom Ansaldo Energia, Avio, BAe, Borg Warner, Honeywell, Pratt & Whitney, Rolls-Royce and Siemens.
As well as manufacturing components for automotive turbochargers, ELE also produces components for industrial gas turbines and aerospace; all of these applications are of course performance-critical. Therefore ELE has the highest level of in-house inspection facilities and processes and it possesses a number of internationally recognised accreditations including TS 16949 for its automotive plant, AS 9100 Rev C / ISO 9001: 2008 for aerospace components, and NADCAP approval for special processes.
ELE approaches product development through a process of ‘concurrent engineering’, working in collaboration with its customers at an early stage. This ensures that the company’s knowledge and expertise helps to develop the ideal process to produce a component at the lowest possible cost.
The ELE story dates back to 1955 when Earby Light Engineers developed a strong reputation as a supplier of compressor blades to Rolls-Royce. Following an MBO in 2000, ELE was formed under new leadership. The team set out to install the finest available technology necessary to compete against the best in the world. Engineering and business processes were developed which ensured that costs, quality and flexibility were of the highest possible standards. In 2004 the company’s old factories were replaced with a modern, purpose-built facility in Colne, Lancashire.
Complementing the UK facility, a modern and efficient factory unit was opened in Trencin, Slovakia. This is now well embedded, with exceptional levels of productivity and quality. The Slovakian plant has the flexibility to produce in excess of 200 different component types at a single site.
If you would like to find out more about ELE Advanced Technologies contact:
Manesh Pandya
Managing Director
Tel: +44(0) 1282 873402
Fax: +44(0) 1282 873403
Mobile: +44(0) 7770 848030
ELE Advanced Technologies Ltd
Cotton Tree Lane
Colne
Lancashire BB8 7BH
Web: www.eleat.co.uk