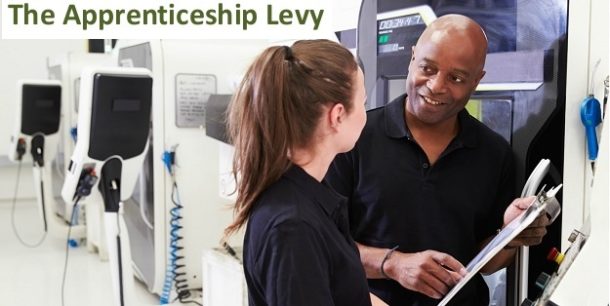
Industry News: Making the most of the Apprenticeship Levy
The UK’s automotive industry has a long-standing history of supporting young people into work through high quality apprenticeships. And not just the major manufacturers, but across companies large and small that form the country’s diverse supply chain to the automotive sector…
As the industry has grown, so has the need for a skilled workforce that is equipped to embrace fast-changing developments in automotive manufacturing. And despite the best efforts across the sector to attract the best and brightest talent, supply has often failed to meet demand.
This skills gap has been covered extensively by the media in recent years, and has shown no signs of abating. A Semta report published earlier this year revealed that in the engineering sector alone, companies in the UK are projected to require 182,000 more skilled workers each year between now and 2020. This will mean that double the amount of apprentices than are currently entering the workforce will be required to meet productivity demands.
A major change is on the way however in the form of the apprenticeship levy, which will be rolled out across the UK in April 2017. For many, the levy is a positive step aimed at ensuring that Britain maintains globally competitive and if delivered effectively, the initiative could be hugely beneficial to automotive supply chain companies.
The apprenticeship levy will apply to all UK employers in both the private and public sectors who pay annual pay bills of more than £3 million. But crucially for most businesses in the automotive supply chain, the Government has also said employers that are too small to pay it – around 98% of those in England – will have 90% of the costs of training paid for by the state. Extra support, worth £2,000 per trainee, will also be available for employers and training providers who take on 16 to 18-year-old apprentices or young care leavers.
Employers are right to consider the financial implications of the levy, and for supply chain companies this is particularly crucial. Training a young person in engineering skills is costly and firms can expect to invest up to £100,000 over the course of a three year apprenticeship programme. At GetMyFirstJob, we have worked with many automotive supply chain companies. Not only have employers told of the positive impact that having apprentices in their company has had on both productivity and morale, but on average these companies will recoup their investment in apprentices in as little as two and a half years. As investments go, this is therefore a pretty fruitful one.
As the levy approaches, it is imperative that employers have a clear vision of what they want to achieve through new apprenticeship schemes. Whether the aim is to develop a long-term work force, or to address a particular short-term skills gap, the levy can help. The first thing we always advise clients to define regarding their levy strategy is to have clear objectives – this enables employers to not only find it is easier to recruit the right candidates for the role, but they can evaluate progression through the training programme and ensure that it is training young people to a high standard.
As an employer, taking an active role in the creation and progression of your training scheme is absolutely vital if you wish to see positive results. Making sure you have regular communication with your training provider and ensuring that the training is tailored to your organisation’s needs and values is vital.
This requires a good level of engagement between employer and training provider which, of course, means both time and resource. If it is achieved though, not only will the three million apprentices the government plan to recruit by 2020 have a bright future ahead of them but the outlook of the UK’s skills gap will be infinitely brighter as well.