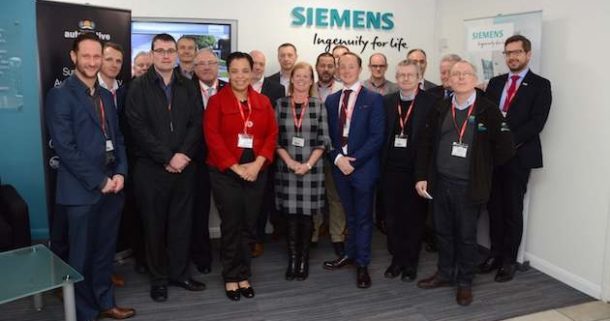
NAA Event Review: Siemens Congleton – How to Digitise your Factory
Throughout the year, NAA members are treated to a wide range of company visits, with the most recent, at Siemens, providing a real-world example of how to apply the latest digital tools to optimise the operation of a factory…
Siemens is a global engineering and technology services company, working in many sectors, and providing many products and services. Siemens Congleton manufactures electric drives for applications such as the conveyor systems that transport your luggage in airports (in case you’re thinking that the few metres of conveyor belt where your bags appear after a flight doesn’t look very much, Munich airport has a 40km conveyer with 20,000 drives). Although this product also has a relevance to the automotive industry, the reason for the NAA’s visit to Siemens was to see how it is digitising its factory to ensure it stays ahead of global competition.
Ian Donald, Head of R&D at Siemens Congleton, gave an introduction at the event, explaining how the company, initially specialising in the electroplating process, was founded in Britain by Sir William Siemens in 1843. Over the 175 years since then the business has grown and now employs 15,000 people in the UK, and has revenue of £6bn.
Ian stressed that the products manufactured by Siemens in Cheshire could be made almost anywhere in the world, potentially at a cheaper cost, so the Congleton site has had to continually re-evaluate its strategy to ensure it offers added value. As a result, a number of ‘themes’ have been introduced, such as communicating with employees in a visual way rather than by KPI spreadsheets, and another theme involves collecting data for business improvement. Much simulation has been carried out, including with the development of a ‘visual twin’ of the facility in the ‘visualisation cave’, in order to achieve a lean factory, which has resulted in significant cost savings.
Siemens has a system known as Mindsphere which captures data, stores it in the cloud, and then accesses the data to extract the information that the business needs. An example of this system in action relates to wind turbines, which can be linked to weather data to predict how much energy will be produced, and therefore whether gas-fired power stations need to be turned on.
NAA networking events also include presentations from member companies, and at Siemens it was the turn of Tom Dawes, CEO of Valuechain. Valuechain may be familiar to some NAA members, as the company was a partner in the NAA’s STRIVE project along with Bentley Motors, VEC and Optis. Valuechain captured Bentley’s data and digitised it, allowing STRIVE partners to access information on tablets rather than via pages of paper-based spreadsheets, resulting in a 48% saving in the time taken to capture, visualise and action data (watch the video at www.striveproject.org.uk).
Valuechain is now taking this concept to the next stage with iQluster, working with organisations such as the APC to develop a visually-based, online network of EV supply chain companies. There are plans to develop a similar visual collaborative platform for NAA members, so watch this space…