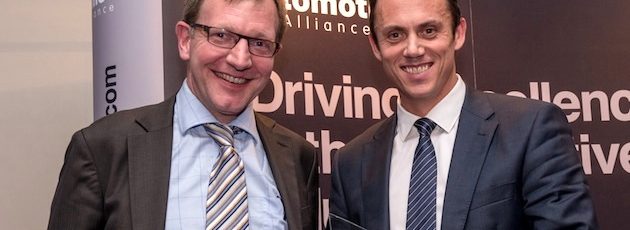
NAA 2013 Award Winner Profile: Supply Chain Growth & Competitiveness Award
Sponsored by SMMT Industry Forum and presented by Chris Lewis, Sector Manager, Automotive
How the award winner was assessed
This was a new award for 2013, and follows on from the activity that Industry Forum has been undertaking in conjunction with the Supply Chain Group of the Automotive Council. The assessment process looked at the strategy for the supply of product, selection of KPIs and values achieved both upstream and downstream, how the demand signal was managed, the capacity risk management, the in-bound logistics package, the sales and order planning process and any other related items. The award is aimed at all companies and looks at how they work with both their customers and suppliers in terms of provision of product.
Winner – ENER-G
ENER-G finances, designs and delivers a range of low carbon, energy efficient technologies. On-site generation technologies, including combined heat and power, heat pumps and anaerobic digestion systems, provide a sustainable, cost effective source of energy. With over 25 years of experience, ENER-G Combined Power undertakes Combined Heat and Power (CHP) projects from the initial design stage to the long term care of the installation.
ENER-G’s cogeneration systems create electricity and heat simultaneously and reduce carbon emissions by around 20%, while cutting electricity costs by approximately one third.
The company’s commitment and dedication to the technology means that it is the number one name in the cogeneration business across Europe.
Following a series of data capture and analysis activities it showed that two areas of supplier quality performance and inventory management had significant potential for improvements, with a third area being added later, as follows:
- 89% of the assemblies required intervention prior to use, the majority coming from two components; after eight months this dropped to 8% and productivity in the department increased by 10.5% linked directly to improved supplier quality.
- Introduction of a rolling 12 month demand window that is refreshed and communicated on a monthly basis took over six months to be introduced and produce positive outcomes, but inventory management was subsequently reduced by 55% and the lead time on key high value items was reduced from 16 weeks to four.
- Introduction of Vendor Management Inventory for fast moving consumables has been in place for 12 months and at each quarterly review the scope of supply has been extended and there has been a significant reduction in inventory and associated transactions.
Craig Allen, ENER-G Group Manufacturing and IT Director, said: “This award is testimony to the robust partnership between ENER-G and our suppliers. By creating a spirit of co-operation and collaboration and sharing accurate information across our supply chain, all parties have benefited. We are delighted to achieve recognition for our joint efforts, which will continue to drive business improvement.”