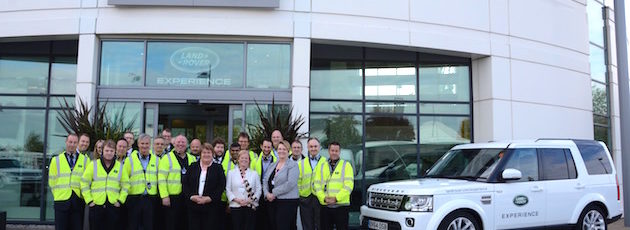
NAA Event Review: Jaguar Land Rover, Halewood, 14 October 2015
The recent NAA tour of Jaguar Land Rover’s production facility at Halewood was fully subscribed within just a few hours of the email going out; here’s a summary of what NAA members experienced…
NAA visitors looked at the layout of the 3.5-mile trim and final line and discussed how JLR uses a barcode system to ensure it builds the 285 vehicles on the line to the exact customer specifications. This can be one of over 380,000 variations where the Range Rover Evoque is concerned.
Visitors discussed JLR’s just in time delivery system and how parts are sequenced onto the line, in particular the importance of having the suppliers of certain parts for the vehicles located on JLR’s supplier park, such as IAC and Magna/Decoma.
Yamazumi was discussed and how JLR manages to break down every standardised work process to ensure it is as efficient as it can be; the dashboard fitting process was used as a physical example of how this is put into practice.
After seeing the right powertrain married with the right body at the right time, and discussing the new diesel Ingenium engine which comes from JLR’s new £500 million facility in Wolverhampton, delegates saw the end of the assembly line to witness a vehicle starting up and driving off every 80 seconds.
NAA members also had an overview of the rigorous quality inspection process in the off-track area, before finally discussing how the cars are distributed via JLR’s railhead (one-third daily) and road transporters (two-thirds daily), and how Halewood is now fulfilling the orders for over 170 countries from one factory.
One of the visitors on the tour was Brian Davies from Colourhouse Masterbatch. This is what Brian had to say about the event: “At Colourhouse Masterbatch Ltd, we have worked very closely with our clients including Jaguar Land Rover on various colours and polymers for the plastic components used in JLR vehicles. Currently we have a wide variety of JLR-approved colours covering nineteen different types of polymer.
“The tour visited the trims and fittings section of the plant. We walked around the site while being given an informative and well-presented explanation at each process stage. Watching the vehicles being built was a very rare opportunity for me, as normally we work with the moulding companies who manufacture the many different plastic components found within the vehicle, and these parts are then supplied into the automotive industry.
“The highlight of my visit was to see the parts coloured by Colourhouse Masterbatch actually being fitted into the vehicles along the production lines, the feeling of pride was very high, in fact I think the smile on my face at that moment was probably as high as the smile will be on the face of the person who takes delivery of that new Jaguar Land Rover vehicle.
“We received the opportunity to visit JLR’s Halewood plant via the NAA and the thought of seeing the vehicles being manufactured was too good an opportunity to miss. From arriving on site the hospitality of both the NAA and JLR staff made me feel instantly at ease and welcome. The pre-tour presentation about the AIP was very informative, raising several questions from the other guests in attendance.”
Another delegate was Andy Graveson, Automotive Team Manager GB, Festo Ltd, who commented: “A tour around such an impressive factory will obviously draw you to the machines, vehicles and the different operations involved, however for me the highlight was more at a people level. Seeing the team working within all the varied functions and the local leadership embedded into the teams was impressive: everyone knowing their role, responsibilities and actions to perform.
“It really made me think about the complexity of logistics and organisation to make things work correctly, on time and to the highest of quality expectations. I have visited many vehicle production lines but the people side of making the production work always amazes me.”
The event at Jaguar Land Rover also included a presentation by Sara Bettsworth from the Automotive Industrial Partnership (AIP). Sara talked about the need to attract more people to the automotive industry, and the skills survey, the results of which will be announced soon. Although the AIP will not be funded by government for the full expected duration, much work has already been done, and a clearing house for apprentices will still be an output.