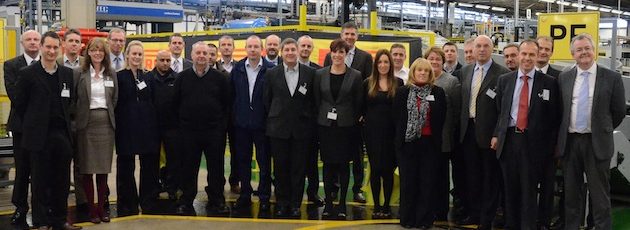
NAA Event Review: Members Networking Meeting, Pirelli Tyres, 20 November 2013, Carlisle
NAA members who attended the recent meeting at Pirelli were left in no doubt that there’s a lot more to the four circular pieces of black rubber that connect your car to the road than meets the eye
The majority of motorists, NAA members amongst them, are likely to give little thought to the one point of contact between their car and the road. However the NAA’s recent visit to Pirelli in Carlisle, which included a factory tour, was a powerful demonstration of why a modern tyre is very much more than just a circular piece of rubber.
NAA members were treated to a presentation about Pirelli, as well as a factory tour – which was described by the tour guides as ‘brief’. However after an hour of the tour, the brains of most visitors were already overflowing with all the information they had learnt about the wide range of processes that are involved in making a tyre.
Pirelli’s factory in Carlisle specialises in SUV tyres – in fact it’s the technological R&D centre for SUV tyres in Europe. In 2011 the Carlisle factory was awarded an RGF grant for development of a range of ‘Green Performance’ SUV tyres – branded as ‘Scorpion Verde’ – which improve fuel consumption and reduce CO2 emissions.
In the 1970’s the factory used to produce tyres for wheels that were typically 13 inches in diameter, now they’re manufacturing tyres for wheels up to 21 inches in size. As well as getting bigger – and heavier (each tyre can now weigh around 15kg) – tyres need to be produced to very tight tolerances, because the driving experience resulting from the finely-tuned chassis of a modern prestige car will be adversely impacted by tyres that have any imperfections.
The Carlisle factory makes tyres for the Range Rover Evoque, which has been a huge sales success (Jaguar Land Rover is taking 140% of its originally anticipated volume, primarily due to the Evoque). Such tyres need to provide the best possible grip on and off road and in different temperatures, whilst also having the lowest possible rolling resistance to assist with fuel economy and emissions – as well as being quiet, durable, and of course affordable. Satisfying such a range of conflicting requirements requires continuous improvement of tyre design and manufacturing processes, and such development was in evidence at the factory.
The factory makes all elements of the tyre itself – no parts are bought in. Once made, all tyres are tested. Any defects can be traced back through the production line thanks to the barcode that every tyre carries.
The Carlisle factory is doing well – no doubt helped by the increasing sales of manufacturers such as Jaguar Land Rover – and this success is being mirrored by other Pirelli factories around the world. SUVs and SUV tyres are certainly in demand in growing markets such as Russia and China, which can only be a good thing for Pirelli and the Carlisle factory.
Find out more at www.pirelli.co.uk
Prior to the factory tour, there was also a Business Excellence sign-up meeting for companies in Cumbria and Lancashire – see Martin’s Business Excellence article for more information.