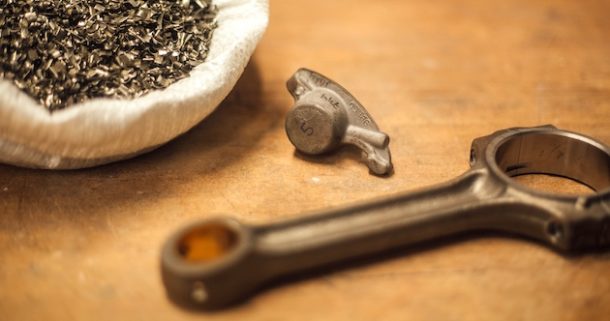
NAA Member News: NAA consortium wins funding for titanium research to lower vehicle emissions
A consortium including the Northern Automotive Alliance (NAA) has been successful in obtaining government funding from Innovate UK for a collaborative research project to use titanium in automotive engines…
The aims of the FAST STEP 3 project are to:
- Achieve lightweighting for automotive engines in order to lower emissions including CO2, NOx and particulate matter, initially at low volume, but it can move into higher volume applications when there is increasing confidence with the product and manufacturing processes.
- Provide growth opportunities for the supply chain, not only within the automotive sector, but also in the wider advanced manufacturing sectors of offshore, rail, aerospace, non-auto engines and defence.
- Enable the metal-forming industry to stay abreast of new technology in alternative metals and use world-leading materials research to assist in halting the decline of the industry within the UK.
High value alloyed titanium swarf will be used as a feedstock for the novel hybrid technology of Field Assisted Sintering Technology followed by one-step hot forging – known as the FAST-forge process – into near net shapes for use in the high strength and good fatigue life applications typically required within an automotive engine.
FAST STEP 3 involves three processes to produce components. Firstly, the FAST process uses titanium swarf to produce a shaped consolidated pre-forged billet. Secondly, a hot forging process produces a near net shape with high strength. Thirdly, final machining produces a component that is net shape and engine-ready. The process will produce titanium at 20% of the cost of current titanium billet, and with minimal waste compared to the 70% waste typically generated from current processes.
The project will manufacture and functionally bench test four components of increasing complexity from both a manufacturing and performance perspective.
The FAST STEP 3 consortium is comprised of Force Technology Ltd, the Northern Automotive Alliance, The University of Sheffield, Transition International, W.H. Tildesley and a vehicle manufacturer. The FAST-forge process developed by the Sheffield Titanium Alloy Research (STAR) team at the University of Sheffield has seen several demonstration projects through the Defence, Science and Technology Laboratory (DSTL) and the Niche Vehicle Network. FAST STEP 3 is the first project that will develop a UK supply chain for the material.
The titanium swarf feedstock, provided by Transition International, will undergo the FAST process at the University of Sheffield. Initially the University will undertake the process on its small-scale lab machine, but later in the project components will be produced from a new 250 tonne machine that will be available at the Henry Royce Institute and the new Royce Discovery Centre in Sheffield.
The products will then be hot forged by W.H. Tildesley, followed by Force Technology Ltd controlling the machining and finishing processes, and undertaking testing to enable the product to be supplied to a vehicle manufacturer. The Northern Automotive Alliance (NAA) is providing project management, dissemination and exploitation support for all partners.
More information on the project can be obtained by contacting the NAA on info@northernautoalliance.com