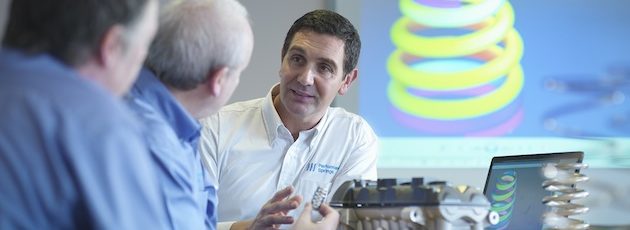
TWISTER is successful in gaining funding for titanium springs project
A consortium pulled together by the NAA and led by Performance Springs has been successful in obtaining government funding through Innovate UK, for a collaborative research project for the development of titanium spring wire and high duty titanium spring applications for use in automotive lightweighting and engine efficiency.
TWISTER (Titanium Wire for Innovative Spring Technologies and Emissions Reduction) is a collaborative research & development programme led by Performance Springs, project managed by the Northwest Automotive Alliance, with other consortium members being Meltech, University of Sheffield, K-Tech and Bentley Motors.
TWISTER seeks a step change in cost reduction of titanium wire for springs by demonstrating an innovative continuous direct manufacturing process applied to both engine valve springs and suspension springs.
The UK-invented process consolidates low cost particulates directly to wire. Titanium springs are more efficient and less dense than steel springs, leading to more efficient combustion engines and lower CO2 emissions. In addition, the energy input and CO2 emissions liberated from the novel consolidation process are significantly lower than the current 30-step batch manufacturing process which includes energy intensive vacuum melting and multiple forging.
By more than halving the cost of titanium wire through leading edge technology, TWISTER will allow its strength and weight properties to be utilised at an economically viable cost, creating major benefits for spring making. New products generated from TWISTER will be affordable and increase the attractiveness to higher volume production vehicles.
Performance Springs is project lead for the £1.6m Innovate UK-funded project, which has six consortium members, four of which are SMEs.